
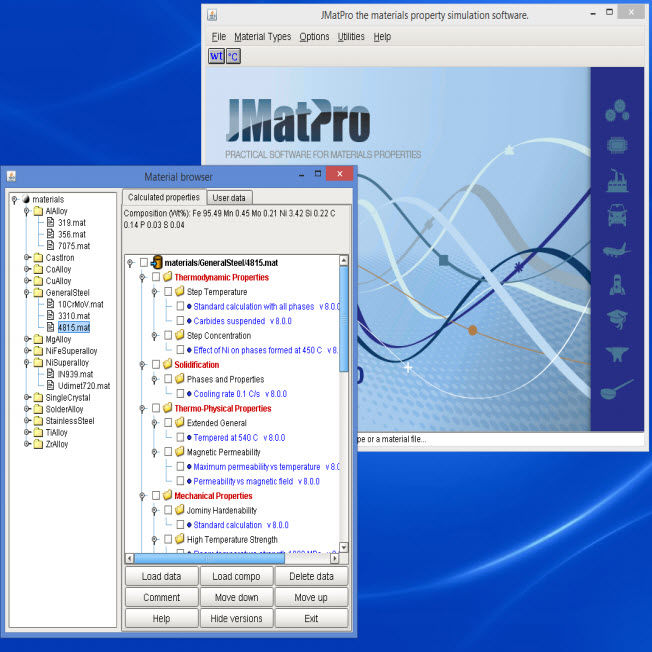
Materialwiss Werkstofftech 41:972–983Īrif TT, Qin RS (2014) A phase-field model for the formation of martensite and bainite. Mukherjee K, Prahl U, Bleck W, Reisgen U, Schleser M, Abdurakhmanov A (2010) Characterization and modelling techniques for gas metal arc welding of DP 600 sheet steels. Zhu B, Chen H, Militzer M (2015) Phase-field modeling of cyclic phase transformations in low-carbon steels. Zhu B, Militzer M (2014) Phase-field modeling for intercritical annealing of a dual-phase steel. Mecozzi MG, Militzer M, Sietsma J, Zwaag S (2008) The role of nucleation behavior in phase-field simulations of the austenite to ferrite transformation. Militzer M, Mecozzi MG, Sietsma J, van der Zwaag S (2006) Three-dimensional phase field modelling of the austenite-to-ferrite transformation. Mecozzi MG, Sietsma J, Van Der Zwaag S (2006) Analysis of γ → α transformation in a Nb micro-alloyed C-Mn steel by phase field modelling. Mecozzi MG, Sietsma J, Van Der Zwaag S (2005) Phase field modelling of the interfacial condition at the moving interphase during the γ → α transformation in C-Mn steels. Mecozzi MG, Sietsma J, Van Der Zwaag S, Apel M, Schaffnit P, Steinbach I (2005) Analysis of the γ → α transformation in a C-Mn steel by phase-field modeling.

Thornton K, Ågren J, Voorhees PW (2003) Modelling the evolution of phase boundaries in solids at the meso- and nano-scales. īoettinger WJ, Warren JA, Beckermann C, Karma A (2002) Phase-field simulation of solidification. In: Shin D, Saal J (eds) Computational materials system design. ĭeWitt S, Thornton K (2018) Phase field modeling of microstructural evolution. Steinbach I (2009) Phase-field models in materials science. Rahul MR, Phanikumar G (2015) Correlation of microstructure with HAZ welding cycles simulated in Ti-15-3 alloy using Gleeble 3800 and SYSWELD. ĭeepu MJ, Farivar H, Prahl U, Phanikumar G (2017) Microstructure based simulations for prediction of flow curves and selection of process parameters for inter-critical annealing in DP steel.
JMATPRO SOFTWARE SOFTWARE
John DM, Farivar H, Rothenbucher G, Kumar R, Zagade P, Khan D, Babu A, Gautham BP, Bernhardt R, Phanikumar G, Prahl U (2017) An attempt to integrate software tools at microscale and above towards an ICME approach for heat treatment of a DP steel gear with reduced distortion. Helm D, Butz A, Raabe D, Gumbsch P (2011) Microstructure-based description of the deformation of metals: theory and application. J Miner Metals Mater Soc 68:70–76Īllison J, Backman D, Christodoulou L (2016) Integrated computational materials engineering: a new paradigm for the global materials profession. Schmitz GJ, Engstrom A, Bernhardt R, Prahl U, Adam L, Seyfarth J, Apel M, de Saracibar CA, Korzhavyi P, Ågren J, Patzak B (2016) Software solutions for ICME. With this ICME workflow, effective properties at the macroscale could be obtained by taking microstructure morphology and orientation into consideration. An ICME-based vertical integration workflow in two stages is proposed.
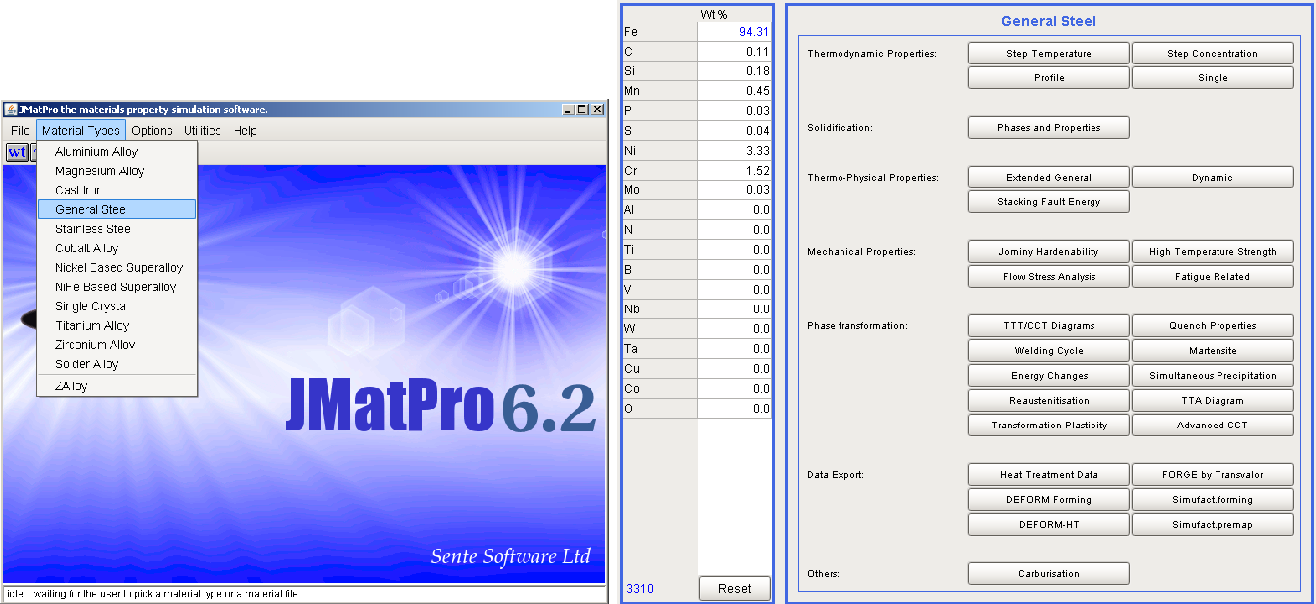
The flow curve from virtual test simulation showed good agreement with the flow curve obtained with tensile test in Gleeble ®. FEM-based virtual uniaxial tensile test with Abaqus ® software was used to calculate the effective macroscale flow curves from the phase-field simulated microstructure. Asymptotic homogenization implemented in Homat ® software was used to calculate the effective macroscale thermo-elastic properties from the phase-field simulated microstructure. A single scaling factor introduced in JMatPro ® software minimized the deviation between calculations and experiments. The phase fractions and the phase transformation kinetics simulated by phase-field method agreed well with experiments. The austenite-to-ferrite and austenite-to-bainite transformations during cooling at HAZ were simulated using the Johnson–Mehl–Avrami–Kolmogorov (JMAK) equation implemented in JMatPro ® software and with phase-field modeling implemented in Micress ® software. The resulting phase transformations and microstructure were studied experimentally.
JMATPRO SOFTWARE SIMULATOR
The time–temperature profile at HAZ obtained from FEM simulation was physically simulated using Gleeble 3800 ® thermo-mechanical simulator with a dilatometer attachment. The macroscale simulation of the welding process was performed with finite element method (FEM) implemented in Simufact Welding ® software and was experimentally validated. An integrated computational materials engineering (ICME)-based workflow was adopted for the study of microstructure and property evolution at the heat-affected zone (HAZ) of gas metal arc-welded DP980 steel.
